np307
Well-known member
Got the frame welded together and then the funnel welded into the frame and all seams sealed up. Next week I'll put the hole in it and then weld up the fittings.Got a fun one going on currently. Going to be a funnel for salt and sugar at a food plant. Going to put a 3" hole through the point and weld in a fitting that can swing between 4 barrels. Everything has to be seal welded. View attachment 352869View attachment 352870View attachment 352872
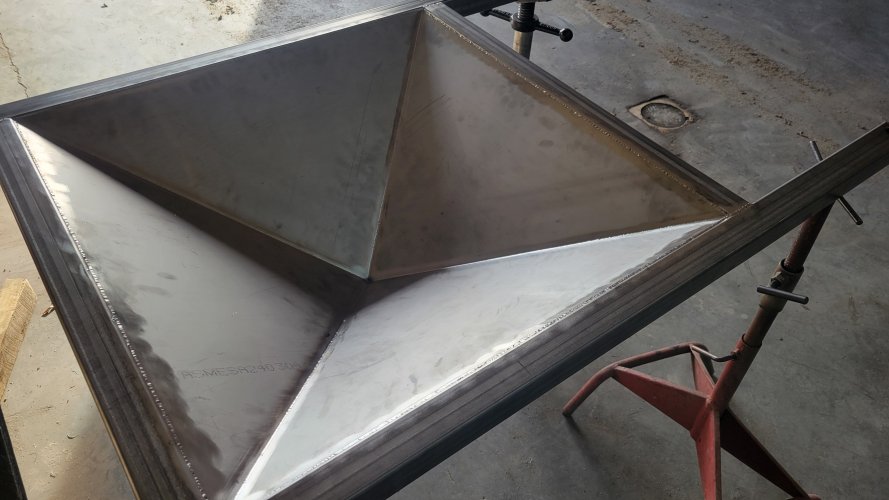
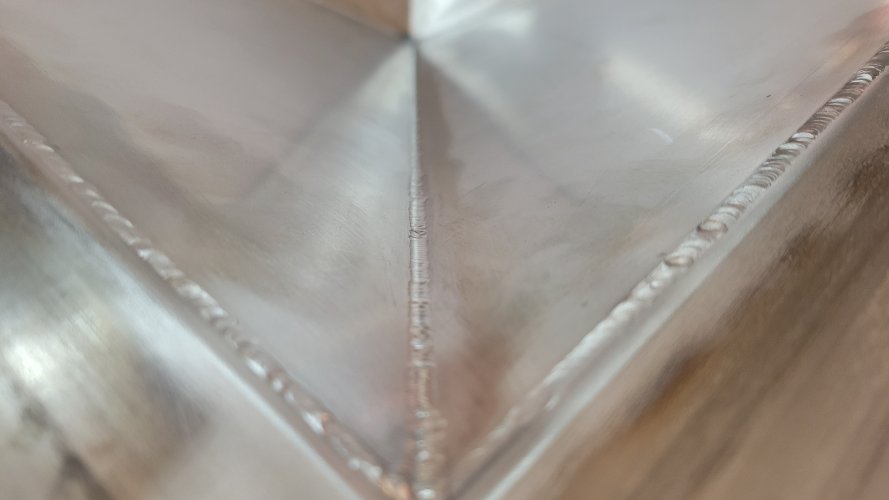