Here's a project, less the crack pipe... Haha! Pretty bad ass! I wouldn't cruise the streets in it BUT I would definitely take it out to the desert with a gremlin revamp project and race, smash, roll and make it a new quality target to shoot at... You know, giveth metals back to mother earth.
Just kidding. We'd torch them first... What? Clean up our garbage? Bah!
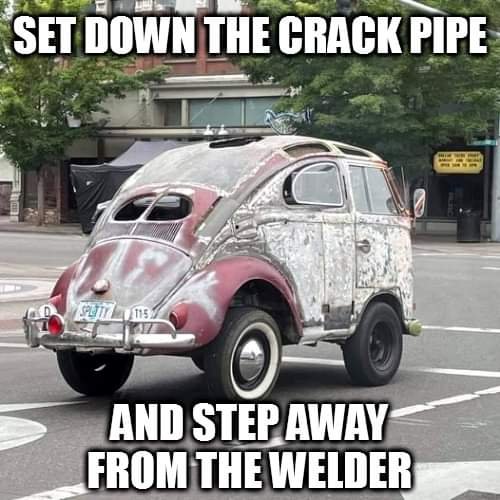
Just kidding. We'd torch them first... What? Clean up our garbage? Bah!
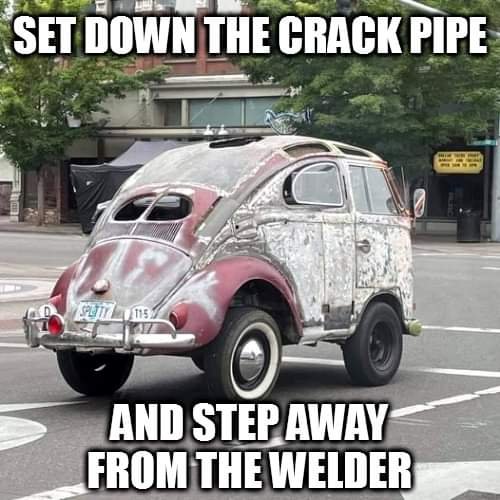